Water and electricity don’t mix, so it’s important to protect electronics that might be exposed to the elements. Whether you should use marine industry certified Printed Circuit Boards (PCBs) depends on the application’s specific requirements and environmental conditions.
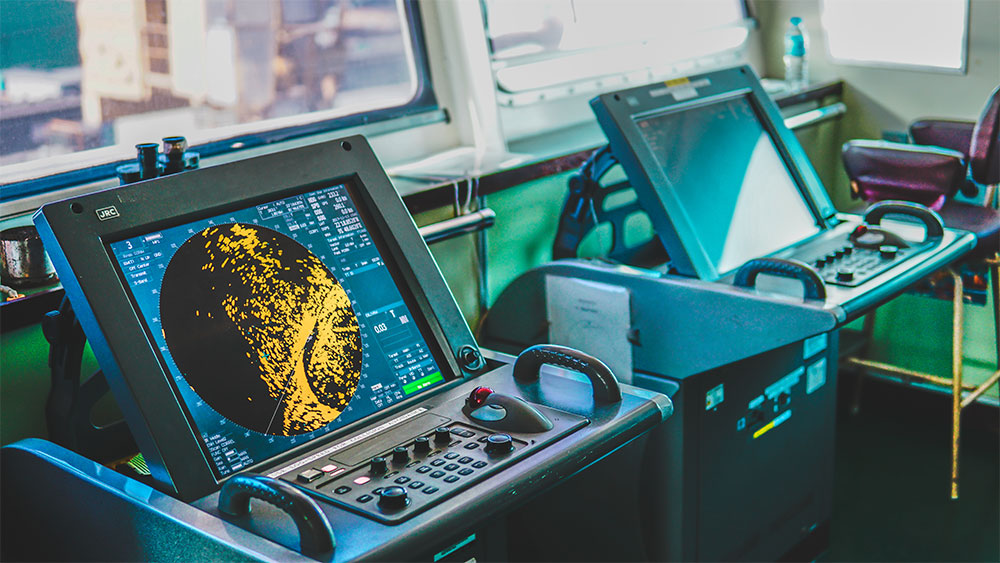
What is a Marine Environment?
Marine environments are found on or near large bodies of saltwater. These include ships, offshore platforms, coastal facilities, and more. Marine environments are challenging due to moisture, saltwater exposure, temperature variations, and vibrations. PCBs must be robust to perform reliably under such stresses.
Here are a few things to consider when determining whether marine-certified PCBs are necessary for your marine application.
Environmental Conditions
Utilizing marine-certified PCBs is crucial if your electronic equipment will be exposed to saltwater, humidity, and other harsh conditions. These PCBs are designed to withstand the corrosive effects of saltwater and provide better resistance to moisture and environmental elements.
Corrosion Resistance
The combination of water, oxygen, and salt is very corrosive. It does more damage to metal than rust. Marine industry-certified PCBs are typically manufactured with corrosion-resistant materials and coatings. This is essential for preventing degradation of the PCB over time due to exposure to saltwater and other corrosive elements. Without that corrosion resistance, unprotected PCBs will turn to toast in marine conditions.
Compliance with Marine Standards
Reliability in Harsh Conditions
Marine environments often involve exposure to vibration, temperature fluctuations, and mechanical stresses. Marine-certified PCBs are designed to withstand these harsh conditions, providing reliable performance over the long term. To paraphrase an old advertisement, marine-certified PCBs are “built to take a licking.”
Long-Term Durability
Because marine environments can be so harsh, marine-certified PCBs are engineered for rugged reliability. This minimizes the risk of failures or malfunctions in critical marine systems.
Product Lifecycle and Maintenance
What is the expected lifecycle of your marine equipment? What are its maintenance requirements? Although the upfront costs of marine industry electronics can be higher, their reliability can recoup your investment. The enhanced durability of marine-certified PCBs may help reduce maintenance needs and increase the longevity of the electronic components.
Cost Considerations
While marine-certified PCBs offer enhanced features and durability, they may come at a higher cost than standard PCBs. Consider whether the added expense aligns with the benefits and requirements of the marine application. It’s a worthy investment if the situation calls for it.
Industry Recommendations
Consult industry guidelines, recommendations, and standards relevant to marine electronics to determine whether marine-certified PCBs are recommended or required for your specific application.
Customization and Consultation
Consult with PCB manufacturers or suppliers experienced in producing PCBs for marine applications. They can guide material selection, coatings, and design considerations for marine-certified PCBs.
Marine industry-certified electronics are essential for applications exposed to harsh marine environments. They are designed to meet specific durability, corrosion resistance, and reliability standards in challenging conditions. When designing electronic systems for marine applications, it’s crucial to assess the environmental factors and industry requirements to determine whether marine-certified PCBs are necessary for the equipment’s success and longevity.